Drill It Right: Best Practices for Efficient and Safe Oil Operations
Discover essential best practices for efficient and safe oil drilling operations, from advanced technology to rigorous safety protocols and waste management.
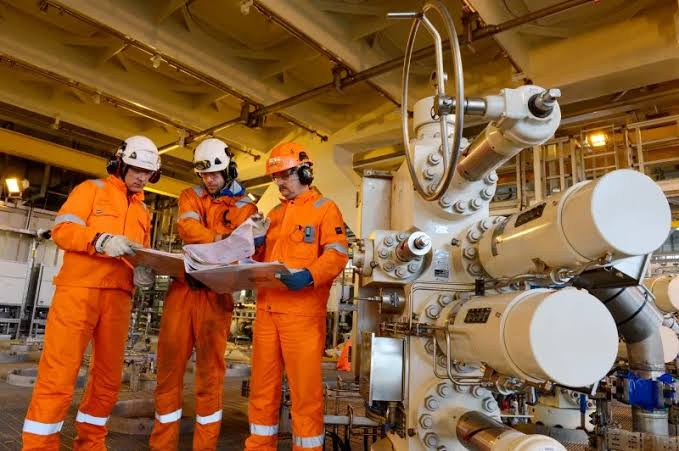
Drilling operations in the oil and gas industry are the backbone of energy extraction. As the demand for oil continues to rise globally, ensuring that drilling operations are both efficient and safe has never been more critical. Whether it’s onshore or offshore drilling, the complexities involved require meticulous planning, advanced technology, and rigorous safety protocols. In this blog post, we’ll explore the best practices for conducting efficient and safe oil operations, focusing on key aspects like technology, safety measures, and operational techniques.
1. Pre-Drilling Planning: The Foundation of Success
Every successful drilling operation starts with comprehensive pre-drilling planning. This phase includes evaluating the geological conditions of the site, designing the well, and assessing the environmental impact. A well-executed planning phase ensures that the drilling team is prepared for any challenges that may arise during the operation.
Site Assessment:
Before drilling begins, geologists and engineers conduct seismic surveys and geological assessments to understand the composition of the ground. This helps in identifying the most effective drilling method, determining the best drilling trajectory, and predicting potential hazards.
Well Design:
A properly designed well is crucial for preventing issues like blowouts, equipment failure, and contamination. The well design considers factors such as the expected depth, rock formations, and fluid pressure to choose the best type of casing and cementing strategies.
Risk Management:
Thorough risk assessments are essential. Potential risks like sudden pressure changes, unexpected geological formations, and equipment failure should be anticipated. This allows for the implementation of mitigation strategies before drilling begins.
2. Using the Right Technology for Drilling Efficiency
Advancements in technology have significantly improved the efficiency and safety of drilling operations. Leveraging these innovations is key to maximizing output while minimizing environmental and operational risks.
Automated Drilling Systems:
Automated systems, such as managed pressure drilling (MPD) and real-time data monitoring, enable teams to make faster and more informed decisions during operations. These systems provide real-time feedback on drilling parameters, allowing operators to adjust in real-time to prevent problems like well control issues.
Directional Drilling:
Directional drilling technology allows operators to drill wells in non-vertical directions, optimizing reservoir access and reducing surface impact. This is particularly beneficial in offshore or tight locations where traditional vertical drilling is not feasible. Horizontal drilling, for instance, can increase the reach of a well, improving production efficiency.
Drilling Fluids:
The selection of appropriate drilling fluids is essential for wellbore stability and for controlling the pressure inside the well. Modern drilling fluids, which can be tailored to specific formations, provide better cooling, lubrication, and wellbore cleaning, reducing downtime and improving efficiency.
3. Rigorous Safety Protocols: Prioritizing Worker Well-Being
Safety in oil drilling operations cannot be overstated. The high-risk nature of the industry makes safety measures an essential component of any drilling operation. Ensuring that workers are well-trained, equipment is regularly inspected, and safety protocols are strictly followed is crucial.
Well Control Systems:
Blowouts, which occur when pressure builds up and exceeds the capacity of the well’s containment system, can have catastrophic consequences. Blowout preventers (BOPs) are critical in preventing such disasters. These devices are designed to seal the well in the event of uncontrolled pressure release. Operators must regularly inspect and maintain BOPs to ensure they function correctly during emergencies.
Emergency Response Plans:
Every drilling site must have a well-defined emergency response plan (ERP) that includes evacuation procedures, spill containment protocols, and emergency contact information. Regular drills and simulations should be conducted to ensure all personnel are prepared for a potential emergency.
Personal Protective Equipment (PPE):
Drilling operations require workers to wear appropriate PPE, including helmets, flame-resistant clothing, gloves, and eye protection. In addition to PPE, continuous safety training and awareness programs help workers understand the risks and precautions associated with their tasks.
Regular Inspections and Maintenance:
Equipment failure is one of the leading causes of accidents in the oil and gas industry. Regular inspections and preventive maintenance schedules ensure that critical equipment, such as pumps, blowout preventers, and cranes, operate at peak efficiency. This also helps detect potential issues before they result in a safety hazard or operational downtime.
4. Environmental Protection: Minimizing the Footprint
The environmental impact of drilling operations is a major concern, especially in sensitive areas like offshore sites and protected lands. Best practices in drilling operations focus on minimizing the environmental footprint while maximizing extraction efficiency.
Waste Management:
Effective waste management systems are crucial for preventing spills and contamination. Drilling operations produce significant amounts of waste, such as drilling mud, cuttings, and chemicals, which need to be handled carefully. To ensure environmental responsibility, these materials must be disposed of in compliance with local regulations. Using filter cloths in waste management can further improve the process by helping to separate solid waste from liquids, reducing environmental impact and promoting more efficient disposal practices.
Environmental Monitoring:
Constant monitoring of air, water, and soil quality around drilling sites helps to detect any signs of pollution. Employing green technologies, such as solar-powered rigs or closed-loop systems that minimize water usage, can further reduce environmental impact.
Flare Minimization:
Flaring, the practice of burning off excess natural gas, has been a common method for managing gas during drilling. However, it contributes to greenhouse gas emissions. Many companies now invest in gas capture technologies or reuse excess gas to power drilling operations, helping reduce environmental harm.
5. Ongoing Training and Team Collaboration
A successful drilling operation depends on the ability of teams to work together effectively. Ongoing training, communication, and collaboration are vital to ensuring both efficiency and safety.
Skill Development:
Continuous training programs ensure that workers stay up to date with the latest techniques and safety protocols. Regularly assessing and developing the skills of the workforce contributes to improved operational performance and safety outcomes.
Collaboration Across Teams:
Successful drilling operations require collaboration between geologists, engineers, safety personnel, and field workers. Clear communication and coordinated efforts help solve problems faster and more effectively, reducing the likelihood of accidents.
In Conclusion
In the oil and gas industry, the phrase “Drill it right” carries significant weight. Efficient and safe operations are paramount, not only for maximizing production but also for ensuring the well-being of workers and protecting the environment. By embracing advanced technologies, adhering to strict safety protocols, and focusing on continuous training and collaboration, the industry can navigate the complexities of drilling operations while minimizing risks and maximizing rewards. With the right approach, drilling operations can continue to thrive, meeting the world’s energy needs safely and efficiently.