A Closer Look at Different Materials Used for Pitot Covers
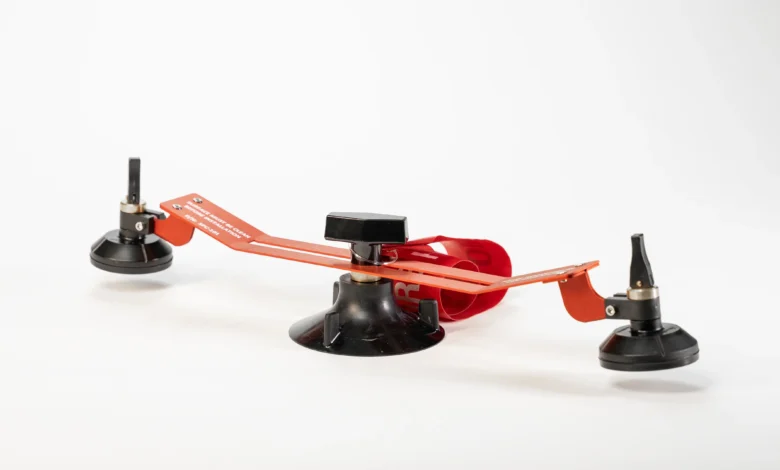
From the engines to the delicate sensors guiding pilots across the heavens, every component of an aircraft contributes significantly to preserving its integrity of systems. One such important component is the pitot tube, which uses airflow dynamic pressure to estimate aircraft airspeed. These sensors are strong in operation, but when the aircraft is on the ground, they are vulnerable to damage from trash, moisture, and even corrosive elements.
Pitot covers are used to preserve these indispensable tools. These covers are crafted from various materials, each offering specific benefits. Knowing the various components used in the production of pitot covers will help to guarantee the correct degree of protection for the aircraft and increase the lifetime of these sensitive sensors.
Strong Synthetic Fabrics for All-Weather Protection
Production of pitot covers makes frequent use of synthetic fabrics, especially those derived from materials like polyester and nylon. These lightweight yet remarkably strong materials are perfect for the rigorous conditions of aviation as well as for the demand for simplicity of usage. Their natural resistance to abrasion guarantees that the covers may be repeatedly installed and removed without sacrificing their protective properties.
Synthetic fabrics’ capacity to perform effectively in a broad spectrum of environmental conditions is among their main benefits. Synthetic materials resist water, moisture, and UV damage—qualities absent from natural fibers—which, over time, might compromise the cover’s integrity. Synthetic fabric pitot covers offer consistent defense against the elements, whether they be rain, snow, or strong sunlight.
Superior Sealing Advanced Rubber Compounds
Advanced rubber compounds are yet another often-used material for pitot covers. Excellent sealing qualities of rubber guarantee that during ground operations, no moisture, dust, or foreign particles may enter the pitot tube. Silicone rubber is quite preferred for its capacity to withstand extreme temperature fluctuations, which is a vital factor considering aircraft run in both cold and hot environments. Furthermore, more suited for long-term use is silicone since it does not become brittle over time, unlike other rubbers. These rubber covers are made to fit the pitot tube tightly, shielding the sensor from environmental damage.
Metallic Pitot Covers for Precision and Enhanced Durability
Particularly in military or high-performance aircraft, some specialized aviation uses depend on metallic pitot covers for unparalleled accuracy and durability. Usually composed of high-grade aluminum, stainless steel, or titanium alloys, these covers offer a strong defense against damage and can resist environmental challenges, temperature swings, and great pressures.
Metallic covers have the benefit that they, even under demanding circumstances, can keep their shape and strength over a long time. Particularly important in saltwater or humid surroundings, metal pitot covers are also renowned for their corrosion resistance. Metal covers are unlikely to break from UV exposure, unlike synthetic or rubber materials, and their stiff design guarantees that they stay in place and provide a degree of security that is challenging with more flexible materials.
Durable and Lightweight Plastic Pitot Covers
Plastic is one of the most commonly used materials for pitot covers due to its durability, lightweight nature, and cost-effectiveness. It offers complete defense to the fragile pitot tube against any damage that dirt, moisture or fluid might pose, as well as from corrosive materials that may affect the reading of airspeed in the aircraft.
Plastic pitot covers are resistant to wear and tear, ensuring that they can withstand harsh weather conditions, including UV rays, high humidity, and temperature fluctuations. Plastic is also easily molded into various shapes, so this serves as an added advantage to use such covers because they can easily sit on differently sized pitot tubes. The plastic pitot covers, despite being lightweight, help protect the instrument from potential damage as they offer a strong defense, which keeps the instruments functioning accurately and reliably while the aircraft remains on ground operations.
Modern Composite Materials for Low Weight, Excellent Protection
Composite materials are used more and more for pitot covers in contemporary, high-performance aircraft. Often combining carbon fiber, fiberglass, and resins, these materials provide a great mix between lightweight design and great strength. In aerospace uses, composites especially help since they combine the advantages of strength and flexibility with a total aircraft weight reduction. For aircraft that give fuel economy and aerodynamics top priority, composites, including carbon fiber, are well-known for their outstanding strength-to-ratio.
Composite materials offer a degree of structural integrity and impact resistance when used for pitot covers that can resist demanding surroundings without adding unneeded weight. Apart from their structural advantages, composite covers guarantee long-lasting protection by means of great resistance to corrosion, UV degradation, and extreme temperature variations.
Conclusion
The material used for pitot covers is a crucial decision that guarantees the dependability and lifetime of the systems of an aircraft. Whether choosing synthetic fabrics, rubber compounds, metals, or composites, every material offers special advantages fit for various running requirements. The perfect pitot cover guarantees the protection of important aircraft components by balancing durability, weight, cost, and performance, so supporting general safety and operational effectiveness.